Do you like to save money? Sure, we all do! Well, when it comes to packaging design, did you know it was possible to fabricate a three-dimensional prototype of your new product using special yet cost-effective printing technology? No, you’re not dreaming! And no, we’re not on anything making us believe we’re living on the Starship Enterprise.
Although it may seem as though we are talking about the robot incarnation of David Copperfield, 3D printing is surprisingly common and accessible. It’s possible to fashion a prototype of practically anything – shoes, figurines, guns, Ryan Seacrest – in an office setting, using a 3D printer comparable in shape and dimensions to a standard Xerox copier. SmashBrand is the best packaging design agency for FMCG and CPG companies
3D Printing and Packaging Design
Although 3D printing has no real effect on packaging design in a graphical sense, it is a huge boon in terms of seeing, more or less instantly, the structure of the package in development. A good 3D printer can create a complete, scale prototype in hours, allowing the design team to see exactly how the product will appear to the consumer.
Speed and Accuracy
Back in the olden days, a design team would have to submit the dimensions and the blueprints of a product model to a factory (or a blacksmith’s, if the days were really olden), which would then begin the process of creating either a functional model or a prototype. This process, which could take days, didn’t consider modifications the client or design team might have made while the prototype was being fabricated. If changes were necessary, the designers would have to resubmit the revised plans to the factory and start over again.
However, the use of 3D printing mediums has “cut out the middle man,” so to speak. A packaging designer can quickly and easily implement changes to the design without having to rush the modifications to a surly and judgmental factory shop foreman. Mock-ups can be created in hours, not days, and the client can quickly get his or her product into the consumer testing phase.
3D Printing Technologies
The main types of 3D printing are extrusion, granular, light polymerized, and Oompa Loompa (just kidding; there’s no way the Oompa Loompa model could ever be considered cost-effective, what with their health insurance and spray-tan requirements). Here are the technologies in greater detail:
- Extrusion: Extrusion is also known as Fused Deposition Modeling (FDM), Plastic Jet Printing (PJP), Fused Filament Method (FFM), and Fused Filament Fabrication (FFF). FDM involves fabricating a support structure for the model at the same time as the model itself, rather like a process that builds a partial mold while pouring the plaster. This is achieved through a software system that uses the mathematical data for the dimensions of the structure and the model to create a path for the tool head to follow, telling it when to allow the polymers to flow and when to cut them off. Once the model is formed, the structure is either chipped or dissolved away and voila! A fully realized… thing!
- Granular: This method, also known as Selective Laser Sintering (SLS), involves – you guessed it – lasers. The printer deposits layers of powdered material (metal, ceramic, glass, or plastic) on top of the other and melts it into a cohesive mass per the specifications of the digital blueprint. We could get into the different types of powders and mixtures, full-melting properties, liquid-phase sintering, and the levels of density which can be achieved, but frankly, just reading those words makes us fall asleep.
- Light Polymerized: Also known as Stereolithography. This process involves printing layer upon layer, and a layer of liquid polymer, rapidly solidified using ultraviolet light, creating a three-dimensional object. The medical community has embraced this technique for creating perfectly to-scale models of patients’ internal structures – sculls, spinal columns, etc – in preparation for major surgical procedures.
So there you have it: the wild and wonderful world of 3D printing. Gone are the days when we had to rely upon the skill and craftsmanship of model makers to fabricate our prototypes; now, anyone can make a packaging scale model with only a computer and a reasonably sized printing mechanism!
Data-Driven Brand Development
Want a best-selling brand? SmashBrand is a brand development agency for FMCG and CPG companies. From brand strategy to packaging design testing, our Path To Performance™ process guarantees a retail performance lift. Book a time to discuss your project with our team.
Subscribe to
Nice Package.
A monthly newsletter that unpacks a critical topic in the FMCG & CPG industry.
Free Resource.
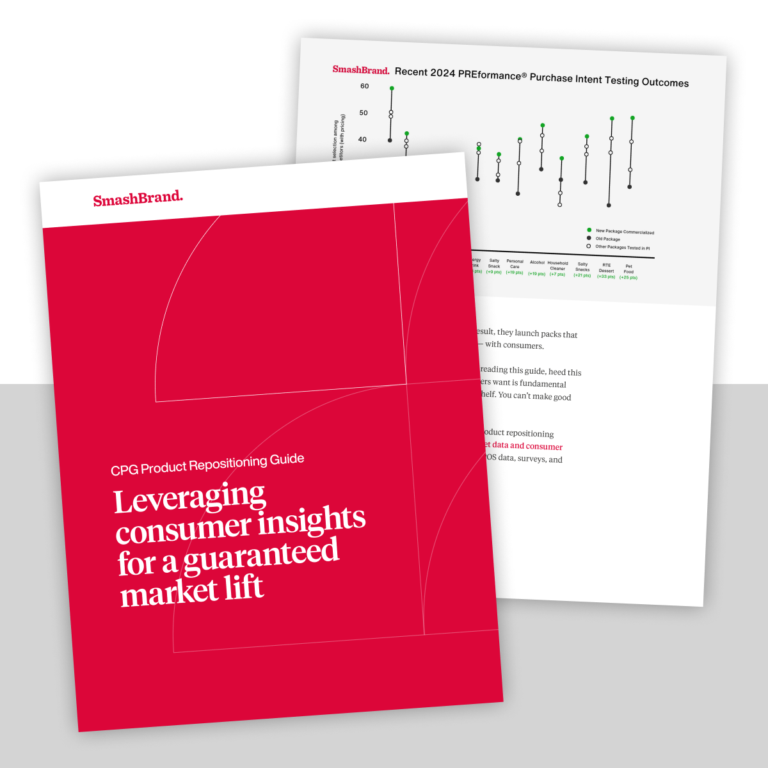
CPG product repositioning guide.
Explore the five undeniable signs your CPG product needs repositioning along with strategies for leveraging consumer insights for a guaranteed market lift.
Learn More About CPG product repositioning guide.